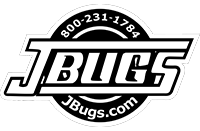
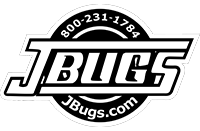
Your cart is currently empty.
For this video we're
going to be installing an alternator on a 1967 for one of the employees here at
the shop. He's had some problems with the generator shaft and the pulley itself
rubbing into the generator.
Alright we've already
gone disconnected the battery now we're going to pull off the breather hose, carburetor
clamp, that way we can pull off the air cleaner. We'll go ahead and take off
the barrel nut, the fuel line, disconnect the choke. Then we'll go ahead and
remove the nuts for the carburetor so we can get the carburetor up and out of
the way.
Make sure to cap off the
fuel line, that way you don't have fuel leaking all over the place. A little
tip for anybody who's got clumsy fingers occasionally. Stick a rag or tape off
the top of the intake manifold that way you're not going to drop any hardware.
Alright now that we've got the carburetor out of the way, we're going to go ahead and disconnect the electrical connections at the generator. We're going to loosen the clamp. We're going to have to go through pull off the shroud screws from the fan shroud backing plate to the back of the generator tin. We're going to have to go ahead and pull off the pulley, belt, and the stand. Alright we're going to go ahead and pull off the fan belt. Usually just takes an adjustable wrench and a flat-head screwdriver sometimes, however because he's got these problems with his generator that might be difficult.
We find some of the culprit a broken pulley, which led to broken shims and did further damage to the generator. We're going to go ahead and pull off the right-hand side spark plug wires. Just to get little bit more access to the fan shroud bolts and generator clamp. We got the clamp out now for the fun part we're going to have to lift up the fan shroud slightly along while we pull off the generators stand so we can go ahead and get the generator backing plate clear of the intake manifold to go ahead and pull this all out.
There are two bolts on
the side of the fan shroud you're going to have to loosen those up to lift the
fan shroud. Don't forget about loosening those otherwise you'll be tugging and
tugging and nothing's going to happen. You can use a screwdriver or shim or
otherwise between the generator and the stand to hold the alternator or
generator in this case, so you can go ahead and get off the last screw for the
backing plate. So that's free.
We can go ahead and disconnect
or rather remove the four 13 millimeter nuts holding the generator stand in
place. Now that we have the generator stand out of place, fan shrouds loosened.
You see that you can pull a generator and fan out of an early car without
pulling off the deck lid. We're going to go ahead and assemble fan backing
plate, fan hub, fans etc. we're going to go ahead and show you how that stuff
is installed.
Starting with the
alternator we're going to have the post at the top breather hole at the bottom,
spacing ring, the final backing plate. A couple of lock walkers and some 10
millimeter head nuts finished that installation there. Note that we do have the
key way already installed. We can go ahead and put the hub itself on if you
notice there's a flat edge on the hub and a circle edge we want the flat edge
pointing towards the fan. We have our fan hub in place followed by the fan. We
have our spring washer; it's got a little wave in there that keeps tension on
the hub nut. Hub nut has a recess for the collar itself as it's tightened down.
Anytime you have a new
fan you want to make certain it's spinning relatively true. No wobble otherwise
that can hit the backing plate and/or it can hit the fan shroud once it's
installed on the fan shroud. Alright now that we have the alternator with the
backing plate and fan installed. We can go ahead and set that in place on the
fan shroud and bolt it up. A lot of times this is going to be a trial and fit
to make certain that the fan itself is not rubbing on the back or the front
side or any side of the fan shroud. What you want to do is go ahead and get it bolted
up. Now that we've got the alternator bolted up to the fan shroud that all four
points. We can spin the shaft, listening for any grinding or scraping
indicating that the fan itself is hitting the shroud. In this case we don't
have any so we are in good luck.
If there were scraping
you need to pull off and pullback out the alternator fan and shim using
generator or alternator pulley shims, shim the fan between the fan itself and
the fan hub to alleviate any of the scraping. We can go ahead and set in the
alternator stand. You'll see we have to change the stand because it's actually
recessed for this large bell here. That's the reason this has to be swapped
out.
We've got a new deflect
plate in place after we scraped off the old gasket. The deflect plate goes in
with the fins pointing down. Sitting at the back of the engine it should say
CCC more or less, that's how you know it's installed correctly. When tightening
down the stand, you want to go in a cross pattern as to not break off the cast
aluminum ears of the stand. We've got all four snug down currently now we can
go back and do a final torque.
With a new alternator
and stand in place, alternator on a fan shroud, fan shroud in place, we can go
ahead and install the two screws at the sides and we can put on the alternator
strap. We've got the strap in place more or less you want to tighten the strap
down until both pieces of metal touch. This strap does need to be very, very
secure as there is actually a lot of load from the pulley on the engine on the
straps. Go ahead and put the nuts or screws rather inside the fan shroud
holding the fan shroud to the cylinder tins. Tighten them up.
Now we've got those
installed we can go ahead and put in the new oil filler. It's going to have a
breather tube that drops down through the engine tin. We're going to put the
road draft tube basically a small rubber boot on the end of that once it's
installed. So we've got the oil filler in place a new gasket underneath it. The
oil filler nut tightening it into the alternator stand, then using the oil
filler nut tool go ahead and tighten it down snugly. Now we can put the oil
filler cap in place.
The breather hose that
goes up to the air cleaner can go up to the port and that portion is done. Now
we can feed the spark plug wires back underneath the alternator and clip them back
in place onto the fans shroud clips and hook them back up to the distributor
cap. Firing order of course is 1 4 3 2 don't get them messed up or you're going
to have a hard time starting.
We can put the carburetor back in place and tighten up its nuts. The accelerator cable can be fed through the barrel nut and you can tighten down the barrel to hold the accelerator cable in place. The fuel line can be reattached to the carburetor and you can tighten its clamp. We're going to go ahead and reconnect the choke to the positive side of the carburetor. Point we can go ahead and install a new quarter inch female terminal on our green wire. That's going to connect to the alternator, you can leave the ring terminal on the large red wire which is going to be the output for the alternator. The green wire plugs into the D plus terminal on the alternator and the red output wire goes to the B plus terminal on the alternator.
With electrical
connections remade to the carburetor and of course our new alternator we can
set our air cleaner back in place. Attach the breather hose from the oil filler
to the air cleaner and tighten the clamp holding the air cleaner to the
carburetor. Alright the last part and probably one of the most crucial parts,
at least to get it right anyway so you don't have the same problems that this
car had previously, is putting on the alternator pulley. Note we've already got
the key way in place. We can put our pulley in place spin it yet again to make
certain nothing is grinding on the fan shroud of course or the pulley back half
against the alternator.
Another real crucial
part is this spacer, make sure it has not fallen out or otherwise in which case
the alternator pulley will actually end up hitting the back side. It is very
important to make sure to use all 10 pulley shims on the pulley. As a starting
point we are going to use five pulley shims in between the pulley halves. We
will first put those on the pulley hub, follow those with the fan belt, then
the outside pulley half.
Next we'll put on the
remaining five shims, the pulley collar, followed by the pulley nut and then we
will tighten the nut. Check the fan belt tension you want about one inch of
play on the fan belt in between the upper and lower pulleys. If the fan belt is
too lose remove shims from in between the pulley halves, if the fan belt is too
tight put more shims in between the pulley halves. Whichever shims are
remaining must go on the outside of the pulley before the pulley collar.
Everything the engine
compartment is now finished next we will move inside the car to complete the
conversion. Underneath rear seat, bolted to the driver side heater channel, you
will see the voltage regulator. The new alternator is internally regulated so
the voltage regulator must be bypassed.
First remove the two
screws holding the voltage regulator to the car. Remove all five wires that are
attached to the voltage regulator. We're going to connect the blue wire that
came from 61 terminal to the green wire that came from the DF terminal with a
quarter-inch terminal connector. Cut off the original terminal end of the three
large red wires. There are originally two wires at the D plus terminal and one
wire at the B plus terminal. Once the ends are cut off strip off about a
quarter inch of wire and crimp on a new quarter inch female terminal end, all
three of these wires will now connect to a quarter inch T connector.
With all the wires now attached to a voltage regulator the installation is now complete and we can reconnect the battery. To test that everything is working properly. Turn the ignition key on but do not start the car. On the speedometer you'll see the two warning lights at the bottom of the speedometer. Make certain that both of these lights come on. One light is for the oil pressure the other light is for the charging system. An internally regulated alternator will not charge if the light does not come on. Start the car. As the oil pressure builds the oil light will go off and when the alternator is charging the charging light will go off.
Copyright © JBugs.
All rights reserved. All images protected by US and International copyright laws. No part of this website may be reproduced, distributed, or transmitted in any form or by any means.
All Prices subject to change without notice or obligation. Not responsible for typographical or photo errors. "Volkswagen", "VW","Beetle", "Super Beetle", "Bus", "Ghia", "Type 2", "Type 3", "Thing", "Rabbit", "Cabriolet", "Jetta", and "Golf" are trademarked by Volkswagen of America and are used for descriptive purposes only.